Wirecrafters is a family-owned business that has always focused on providing our customers with creative solutions for their safety, security, and storage needs while meeting commitments with exceptional quality by people who care. One of the solutions we’ve provided to businesses worldwide is our state-of-the-art machine guard system, the RapidGuard II®. Regarding this system, safety and security are two of the major standards at stake. It’s essential to recognize that the only way to maintain these standards is to understand the proper machine guarding requirements.
Machine Guard OSHA Standards
You know what OSHA is, but you may not know all of the standards and regulations they have in place. Here’s what they have to say about machine guarding standards:
One or more methods of machine guarding shall be provided to protect the operator and other employees in the machine area from hazards such as those created by point of operation, ingoing nip points, rotating parts, flying chips and sparks. Examples of guarding methods are – barrier guards, two-hand tripping devices, electronic safety devices, etc.
The point of operation of machines whose operation exposes an employee to injury shall be guarded. The guarding device shall be in conformity with any appropriate standards; therefore, or, in the absence of applicable specific standards, shall be so designed and constructed as to prevent the operator from having any part of his body in the danger zone during the operating cycle.
(iii) Special hand tools for placing and removing material shall be such as to permit easy handling of material without the operator placing a hand in the danger zone. Such tools shall not be in lieu of other guarding required by this section, but can only be used to supplement protection provided.
The following are some of the machines which usually require point of operation guarding:
- (a) Guillotine cutters.
- (b) Shears.
- (c) Alligator shears.
- (d) Power presses.
- (e) Milling machines.
- (f) Power saws.
- (g) Jointers.
- (h) Portable power tools.
- (i) Forming rolls and calendars.
As you can see, these standards are specific and vital for the safety of your team and clients. If you’re working around machinery in an industrial facility, chances are you have machines that require guarding. Before anything else, you want to ensure that your facility follows OSHA standards to maintain your operations.
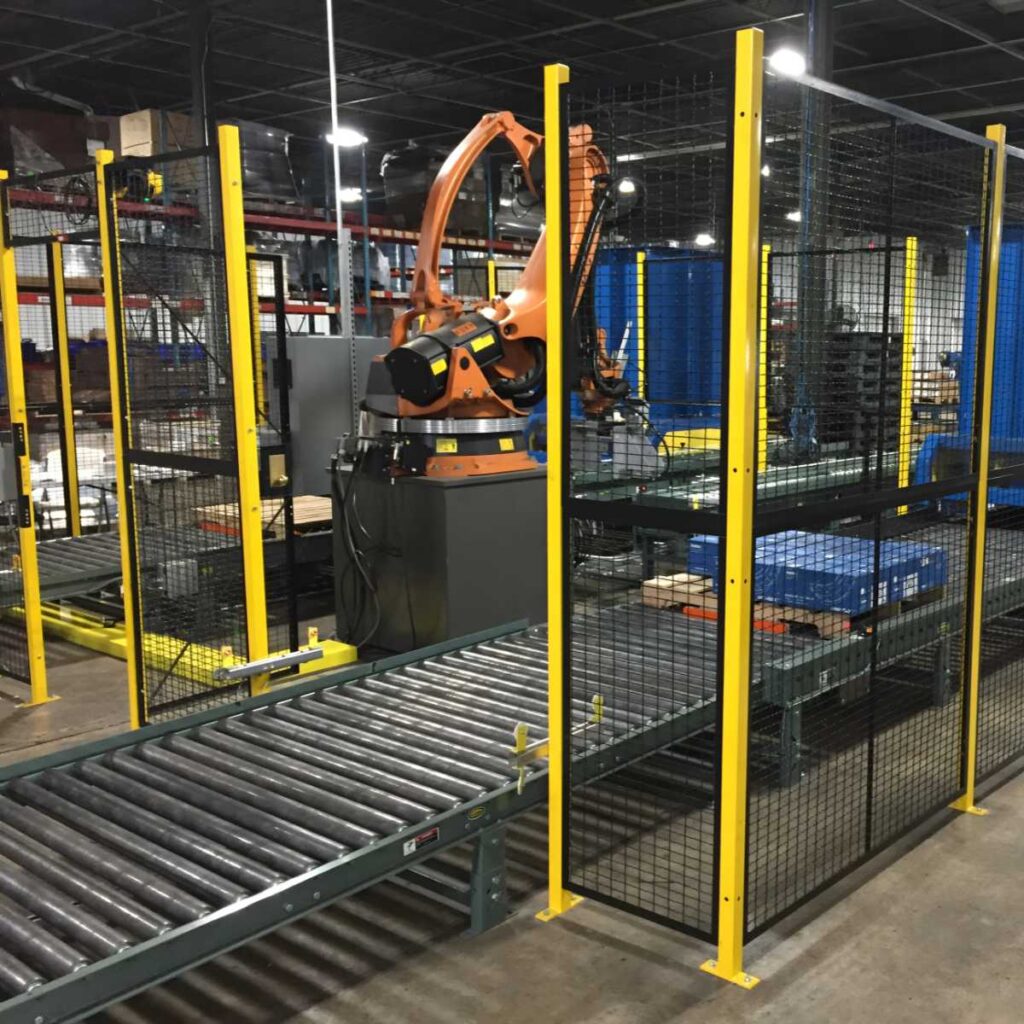
Proper Distance and Materials for Machine Guarding
Any machine that is within seven feet of an operator or workstation needs to be guarded. This accounts not only for machinery like conveyor belts but also for machinery that may have flying sparks or projectiles that could be dangerous to operators in the area. A standard partition must be at least 33.46 inches from the machine when installing the guarding.
While metal, plastic, and wood are all viable machine guarding materials if they protect from hazards, metal is undoubtedly the safest. Our wire mesh material is made of 10 gauge welded metal wire and patterned in a 1 1/4″ SQ (center to center). The mesh is then welded into a 1 1/4″ x 1 1/4″ 13 gauge roll formed angle. This creates the strongest and safest machine guarding the industry has to offer!
WireCrafters’ Machine Guarding Standards
While the industry standard partition must be at least 33.46 inches from the machine in order to stay within regulations, the RapidGuardII® follows regulations at a minimum distance of 4.7 inches! We are well-versed in the machine guard standards your industry and OSHA require, leading us to create the most effective option for your facility.
Here are some of the safety standards that our machine guarding always follows:
- ANSI B11.19-2019
- Performance criteria for safeguarding
- ISO 14120:2015
- Safety of machinery – Guards – General requirements for the design and construction of fixed and movable guards.
- OSHA 29 CFR 1910.212
- Occupational Safety and Health Standards – General Requirements for all Machines
- ANSI B11.0-2020
- Safety of machines: General requirements for risk assessment
- ANSI/RIA R15.06-2012
- American National Standard for Industrial Robots and Robot Systems – Safety Requirements [U.S. National Adoption of 10218-1,2:2011]
- RIA TR R15.306-2016
- [Technical Report] Task-based Risk Assessment Methodology
- CAN/CSA Z434-14 (R2019)
- Industrial Robots and robot systems [Canadian adoption of 10218-1,2:2011, with Canadian deviations]
- ISO 13855:2010
- Safety of machinery – Positioning of safeguards with respect to approach speeds of parts of the human body [being updated]
- ISO 13857:2019
- Safety of machinery – Safety distances to prevent hazard zones being reached by upper and lower limbs
- ISO 14119:2013
- Safety of machinery – Interlocking devices associated with guards – Principles for design and selection [being updated]
Following each of these standards plays a vital role in our dedication to the safety of our team and yours. It can be easy for many organizations to follow a few standards but ignore others. At Wirecrafters, we understand that these standards exist for a reason, and abiding by them is our number one priority.
At WireCrafters, above all, we are concerned with the safety of your employees. RapidGuard™ II was designed by a unique team of WireCrafters engineers commissioned to think differently in order to solve common operational issues in the industrial and material handling industries. Over the years, we have continued to exemplify trendsetting innovation and superior customer service.
We know you have a lot on your plate, and ensuring your facility is up to all of the proper standards can be overwhelming. We’re here to help lighten your burden and protect your team. So, if you’re in need of new machine guarding in your facility, contact WireCrafters today!
To learn more about WireCrafters, visit www.wirecrafters.com or follow us on YouTube, LinkedIn, Facebook, and Instagram.
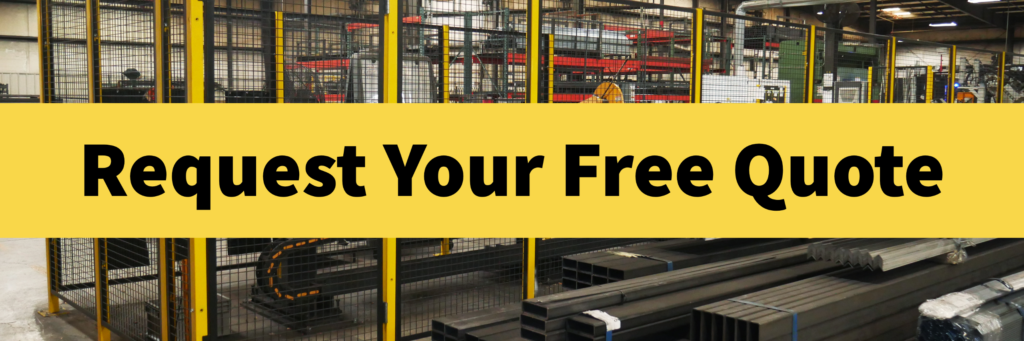